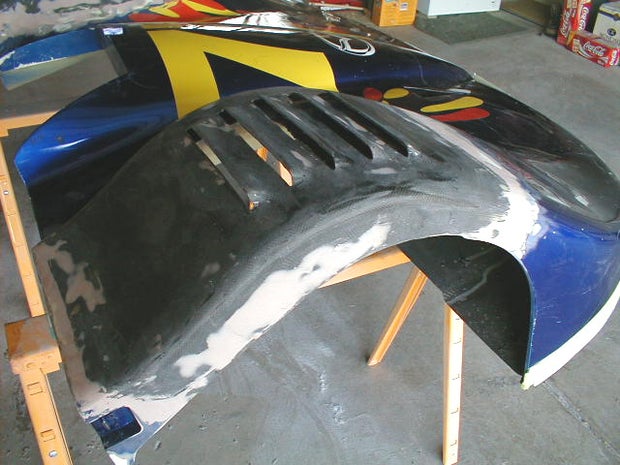
We are a well rounded fiberglass shop that offer a wide range of skills to build your dream race car. But theres also the cost of the consumables of the process like mold wax solvents and sand paper.
Learn how to make your own one-of-a-kind professional quality show car fiberglass body.
Making fiberglass car parts. This video segment will show you how to make a fiberlgass mold. After 2 years of waiting for an opportunity to re-visit this process I was finally able to do a video on the mold making process. CHECK OUT OUR NEW FIB.
Traditionally fiberglass parts are coated with gel coat a wax rich polyester resin. Gel coat is thick heavy and brittle so it doesnt take a lot of it. But it provides excellent protection against UV damage from the sun.
It goes on like thick paint and cures in a few minutes. Fiberglass can be used to make a copy of an existing automotive body part to repair damaged parts or as a foundation for custom-body panels. Fiberglass is the casting material of choice for many auto body workers.
It can be formed into any variety of complex shapes and you can buff its surface as smooth as a commercially manufactured body part. The copy made of fiberglass is referred to as a mold. Lay mat on or in your form and spread the resin mixture over it with a disposable paint brush.
The mat or cloth will seem to melt into the resin as you spread it and you can use the brush and additional coats of resin to build up the layer of fiberglass to a thickness of up to 14 inch 06 cm. Located in Naperville IL Glasstek has been manufacturing fiberglass body components for over 25 years we have over 40 years experience in the automotive fiberglass industry. Most of our parts are made to order although we do try to stock a very limited selection of the parts we make.
Call or e-mail to find out if we have the part or parts you need in stock or for an estimated time to make the parts you are looking for. Owned and operated by Christopher Ross since 2006 and in 2015 we expanded our business to integrate the next phase of are growing company. We are a well rounded fiberglass shop that offer a wide range of skills to build your dream race car.
We build fiberglass body shells for a variety of different vehicle makes and models. We can also make over a 1000 different parts repair fiberglass race car bodies mount bodies do sheet metal work custom make parts mig welding tig welding. The first step is to cut a pattern from blue insulation foam and wrap it with clear packing tape.
Next cover the taped pattern with a mold release wax. Now cover the pattern with woven fiberglass cloth and wet out the resin. Make sure to leave a section uncovered- this is where the foam will be melted.
This Is the Place For High Quality Fiberglass Components For Street Cars And Race Cars. Click Here to View Catalog. Welcome to Our website.
VFN has been a leader in this industry for over 46 years Our Mission is to make quality lightweight products that handle the stress and abuse that comes with Drag-racing and also keep the detail that. Cover the shaped styrofoam in adhesive resin applied with a paint brush and cover the shape with fiberglass cloth. Press the fiberglass cloth into the styrofoam with a hard roller.
Allow the piece to dry for 12 hours. Repeat the process until four layers of fiberglass cloth have been applied to the foam sculpture. To reinforce the joint I then applied a couple of layers of 12 oz.
Fiberglass tape around the outer edge of the cockpit fairingcar body seam. Using epoxy mixed with 410 Microlight to create a fairing compound I smoothed out the surface then sanded it to create the final shape. For someone making fiberglass car parts the costs include the materials like the dry fabric and the resin and catalyst.
But theres also the cost of the consumables of the process like mold wax solvents and sand paper. Mustang fiberglass Bill Maier first started making fiberglass parts for 1965-67 Mustangs in the early 1970s in San Leandro California. He looked at the racing aprons on the 65 Shelbys which deleted the stock bumper and found a more practical solution.
Learn how to make your own one-of-a-kind professional quality show car fiberglass body. There wont be another one anywhere like it. Youll see the creation of Fritzs latest fiberglass body show rod the Baja Bandeeto.
Fritz starts with a hand built chassis made from junk parts and scrap steel. He uses a motor and parts from the junkyard. Fiberglass the Wonder Material of the 1950s was the Carbon Fiber Of Its Day.
People Flocked To Car Shows To See Sports Cars Built From The New Lightweight Material Fiberglass Just Like They Do Today To See A Sports Car Built Using Carbon Fiber. Mold making and fiberglass layup Step 1. Carve out a big chunk of the foam to match with the fuselage and then cut out the sides using a carpet or kitchen knife.
Rough cut the sides with the knife to complete the shape and sand to achieve the perfect shape. This step can be adequately done in an hour or half. US Body Source inc.
Custom hoods tilt front ends race car parts ram air hoods fenders doors trunk lids fiberglass body parts full bodies and more. Great Prices Availability. Dec 25 2015 - Maier Racing started making fiberglass parts in the early 1970s.
Bill Maier started in San Leandro California making gravel shields for the 1965 1967 Mustangs. Throughout this cars life there have been some bumps and scrapes which have caused some damage to the body. One of the worst was a split under the rear deck on the rear firewall between the gas tank and the interior of the car.
A previous owner had attempted a fiberglass repair which we were able to remove with just the twist of a screwdriver.